Flow Drilling, also called Friction Drilling or Thermal Drilling is a holemaking technique that has been used for decades across a wide range of industries. At Thompson Fabricating, we use this method instead of conventional drilling, eliminating the need for additional hardware, such as rivet nuts, to assemble our mechanically fastened aluminum component rail systems most efficiently.
We have chosen to go this route because Flow Drilling provides these key advantages:
1) Stronger connections between components that makes our rail systems safer for customers to use; 2) Higher reliability throughout the drilling and tapping process; 4) Smoother fit and finish for joining rail system components; and 5) Higher reliability of the rail system’s field performance.
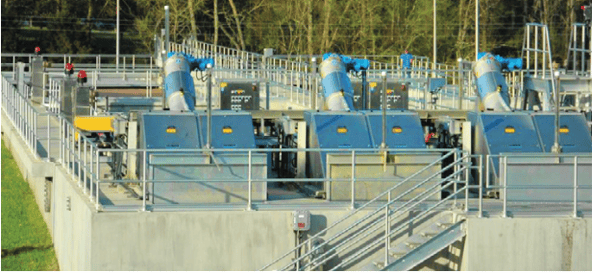
How Thermal Drilling Works
As an alternative to more widely used drilling methods, Flow Drilling is a 4-step process that uses a bit made of a highly heat-resistant material such as tungsten carbide (aka cemented carbide).
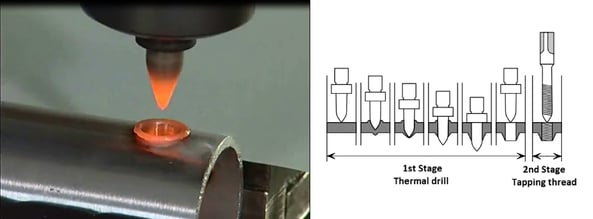
In Step 1, the bit—held by the holder—is positioned on the workpiece. It rotates at a high speed and under high pressure. The friction and pressure resulting from this operation heats the material, which in our case is Schedule 40 6105 Aluminum Pipe. The process generates “local” heat production which softens and displaces the material without removing a chip and without melting the metal.
Step 2 consists of the bit rotating at speeds up to 9,000 rpm and simultaneously applying high pressure force (up to 3,000 N) to the material. This phase of the operation allows the tool to "sink" through the tube and make a hole in the workpiece to form a sleeve around the hole. That sleeve is up to 3X the material’s original thickness.
The sleeve’s metal lip around the hole makes connections stronger than ones formed with welds, weld nuts with bushings, or rivet nuts, sometimes referred to as rivnuts. As a result, our handrail systems last longer and provide a higher degree of safety compared to systems connected by using traditional fastening methods.
After the bit has penetrated the material, Step 3 occurs. At this stage of the operation, the drill reduces the fastener’s rotation speed and force applied to the workpiece. These decreases in speed and pressure allow the tap to drive through the material and form threads without cutting the material.
Step 4 consists of installing the fastener with the required amount of torque to optimize the component rail system’s functionality.
Our use of Flow Drilling, Friction Drilling, Thermal Drilling – call it what you will – is one of the many ways we maximize the quality, value, and safety of the engineered vertical access and safety products we manufacture for applications in the utility, industrial, construction, and maintenance markets. That commitment to providing our customers with the best of everything in engineered and fabricated products has been part of our company culture for the past 70 years, and it remains at the heart of all we do.
To maximize the safety and operating life of your component rail system…